Articles & Issues
- Conflict of Interest
- In relation to this article, we declare that there is no conflict of interest.
-
This is an Open-Access article distributed under the terms of the Creative Commons Attribution Non-Commercial License (http://creativecommons.org/licenses/bync/3.0) which permits unrestricted non-commercial use, distribution, and reproduction in any medium, provided the original work is properly cited.
Copyright © KIChE. All rights reserved.
All issues
걱막식 과산화수소 제조에 관한 연구
Manufacture of Hydrogen Peroxide by Electrolytic Process
HWAHAK KONGHAK, August 1965, 3(2), 133-141(9), NONE
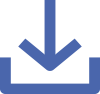
Abstract
This paper was undertaken to study a wide variaty of problems concerned with manufacturing Hydrogen Peroxide. By means of the laboratory experiments they were observed, a critical and comprehensive data, and optimum conditions for preparing Hydrogen Peroxide.
The laboratory experiments were divided to three steps as follows.
The first step; the diaphragm electrolytic process, in which ammonium peroxy-disulfate was formed on the anode by oxidation electrolytic.
The second step; the Hydrolysis and Distillation process, in which Hydrogen Peroxide was formed by pure chemical reaction in the heated oxygenated anolyte, then the H2O produced was separated directly from H2O2 anolyte mixture under vacuum distillation.
The last step; the concentration of dil. Hydrogen Peroxide by fractional distillation under vacuum.
The cell (1 liter glass cylinder) was consisted of two rectangular platinum anode lines and a rectangular platinum cathode plate dipped into a cylindrical porous ceramic diaphragm set in the center of the cell. Anolyte chamber (outside the diaphragm) was filled with 650 ml solution containing 260 gr. of ammonium sulfate and 200 gr. of sulfuric acid per liter, and catholyte chamber (in the diaphragm), 125 ml. solution containing 230 gr. of ammonium sulfate and 280 gr. of sulfuric acid per liter.
The electrolytic experimental data were demonstrated in Tabel 1 to 7, and their curves, on Fig. 9 to 15.
Concentration process data were demonstrated in Table 8 to 10, and their curves, on Fig. 16 to 19.
According to above data, maximum eEff. was observed 83 %, maximum eEff., 34 %, and maximum concentration of H2O2 56 %.
The laboratory experiments were divided to three steps as follows.
The first step; the diaphragm electrolytic process, in which ammonium peroxy-disulfate was formed on the anode by oxidation electrolytic.
The second step; the Hydrolysis and Distillation process, in which Hydrogen Peroxide was formed by pure chemical reaction in the heated oxygenated anolyte, then the H2O produced was separated directly from H2O2 anolyte mixture under vacuum distillation.
The last step; the concentration of dil. Hydrogen Peroxide by fractional distillation under vacuum.
The cell (1 liter glass cylinder) was consisted of two rectangular platinum anode lines and a rectangular platinum cathode plate dipped into a cylindrical porous ceramic diaphragm set in the center of the cell. Anolyte chamber (outside the diaphragm) was filled with 650 ml solution containing 260 gr. of ammonium sulfate and 200 gr. of sulfuric acid per liter, and catholyte chamber (in the diaphragm), 125 ml. solution containing 230 gr. of ammonium sulfate and 280 gr. of sulfuric acid per liter.
The electrolytic experimental data were demonstrated in Tabel 1 to 7, and their curves, on Fig. 9 to 15.
Concentration process data were demonstrated in Table 8 to 10, and their curves, on Fig. 16 to 19.
According to above data, maximum eEff. was observed 83 %, maximum eEff., 34 %, and maximum concentration of H2O2 56 %.