Articles & Issues
- Language
- korean
- Conflict of Interest
- In relation to this article, we declare that there is no conflict of interest.
- Publication history
-
Received June 28, 2006
Accepted July 26, 2006
-
This is an Open-Access article distributed under the terms of the Creative Commons Attribution Non-Commercial License (http://creativecommons.org/licenses/bync/3.0) which permits unrestricted non-commercial use, distribution, and reproduction in any medium, provided the original work is properly cited.
Copyright © KIChE. All rights reserved.
All issues
근임계수 가수분해 공정을 이용한 TDI 공정 폐기물로부터 TDA 회수 공정 최적화
Optimization of TDA Recycling Process for TDI Residue using Near-critical Hydrolysis Process
한화석유화학 중앙연구소, 초임계사업그룹, 305-804 대전시 유성구 신성동 6
SCWO Business Group, Hanwha Chemical R&D Center, 6 Shinsung-Dong, Yusung-Gu, Daejeon 305-804, Korea
jhhan@hanwha.co.kr
Korean Chemical Engineering Research, December 2006, 44(6), 650-658(9), NONE Epub 2 January 2007
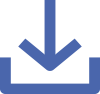
Abstract
통계적 실험계획법을 이용하여 TDI 공정에서 발생하는 고체 폐기물(TDI-R)을 근임계수로 가수분해하여 TDA로 재활용하는 연구를 진행하였다. Batch 반응기를 이용한 실험으로부터 TDA 수율에 미치는 주요 인자들의 영향과 교호작용을 확인하였고, pilot plant를 이용한 연속공정 실험을 통해 TDA 수율과 공정 변수들의 상관 식을 도출하였다. TDA 수율에 영향을 주는 주요 인자들은 반응온도, 촉매 종류 및 농도, 물과 TDI-R의 중량비(WR) 등이 유효한 것으로 파악되었다. 반응 온도와 촉매 농도가 증가할수록 TDA 수율은 감소하였고, WR이 증가할수록 수율은 증가하였으며, 촉매로는 Na2CO3보다 NaOH를 사용하는 것이 효율적이었다. 주요 인자들의 교호작용으로는 촉매농도와 반응온도, WR과 반응온도, 촉매 종류와 반응시간 등이 유효한 것으로 파악되었다. 아임계 온도인 300 ℃에서는 촉매 농도 영향이 작지만 초임계수 온도인 400 ℃에서는 촉매 농도가 증가할수록 수율이 감소하였다. 반면 300 ℃에서 WR이 증가하면 수율이 증가하지만 400 ℃에서는 영향이 나타나지 않았다. Pilot plant를 이용하여 scale-up에 필요한 공정 변수의 최적화 실험을 실시하였다. 공정의 경제성, 효율성을 고려하여 공정변수로는 촉매농도와 WR을 정하였고, 중심합성 설계법을 이용하여 TDA 수율에 미치는 인자들의 영향을 파악하였다. 촉매 농도에 따라 수율은 증가하며, 촉매 농도가 낮을때는 WR이 2.5 이하에서 수율이 최대값을 보인 후 WR이 증가함에 따라 수율이 감소하지만 촉매 농도가 증가하면서 최대값을 보이는 WR이 증가하는 경향을 보였다. Pilot plant 실험 결과를 회귀 분석하였으며 TDA 수율을 예측할 수 있도록 촉매 농도와 WR이 변수인 2차 식으로 상관식을 도출하였다.
The recycling of TDA from solid waste of TDI plant(TDI-R) by near-critical hydrolysis reaction had been studied by means of a statistical design of experiment. The main and interaction effects of process variables had been defined from the experiments in a batch reactor and the correlation equation with process variables for TDA yield had been obtained from the experiments in a continuous pilot plant. It was confirmed that the effects of reaction temperature, catalyst type and concentration, and the weight ratio of water to TDI-R(WR) on TDA yield were significant. TDA yield decreased with increases in reaction temperature and catalyst concentration, and increased with an increase in WR. As a catalyst, NaOH was more effective than Na2CO3 for TDA yield. The interaction effects between catalyst concentration and temperature, WR and temperature, catalyst type and reaction time on TDA yield had been defined as significant. Although the effect of catalyst concentration on TDA yield at 300 ℃ as subcritical water was insignificant, the TDA yield decreased with increasing catalyst concentration at 400 ℃ as supercritical water. On the other hand, the yield increased with an increase in WR at 300 ℃ but showed negligible effect with WR at 400 ℃. The optimization of process variables for TDA yield has been explored with a pilot plant for scale-up. The catalyst concentration and WR were selected as process variables with respect to economic feasibility and efficiency. The effects of process variables on TDA yield had been explored by means of central composite design. The TDA yield increased with an increase in catalyst concentration. It showed maximum value at below 2.5 of WR and then decreased with an increase in WR. However, the ratio at which the TDA yield showed a maximum value increased with increasing catalyst concentration. The correlation equation of a quadratic model with catalyst concentration and WR had been obtained by the regression analysis of experimental results in a pilot plant.
Keywords
References
Gagnon SD, Bananto SA, “Recovery of Products from Toluenedi Isocyanate Residues,” U.S. Patent No. 5,902,459 (1999)
Koch HJ, “Recovery of Amines,” U.S. Patent No. 3,128,310 (1964)
Michio I, Shinji O, “Decomposition of Solid Residue,” Jpn. Kokai Tokkyo Koho, JP2000-136264 (2000)
Treybig DS, Hock KJ, Kent VA, Dai SA, “A Process for Recovering Toluene Diaamine from Toluene Diisocyanate Distillation Residues,” PCT Patent No. WO 00/68180 (2000)
Kim YC, Lee SB, Yook SH, Choi IY, Lim YM, “A Process for Toluene Diamine Recovery,” Korea Patent No. 10-0383217 (2003)
Nagase Y, Fukuzato R, “Method of and Apparatus for Decomposing Wastes,” U.S. Patent No. 6,255,529 (2001)
Yuk HM, Park JH, Park S, Lee CH, HWAHAK KONGHAK, 41(2), 249 (2003)
Nagase Y, Yamagata M, Kobelco Technology Review, 22, 11 (1999)
Sato O, Arai K, Shirai M, Catal. Today, 111(3-4), 297 (2006)
Lee WY, Park SD, Yeo SD, HWAHAK KONGHAK, 39(2), 257 (2001)
Shanableh A, Water Res., 34, 945 (2000)
Nordquist AF, Pierantiozzi R, “Process for the Disproportionation of Alkylated Aromatic Primary Amines,” U.S. Patent No. 4,935,545 (1990)
Koch HJ, “Recovery of Amines,” U.S. Patent No. 3,128,310 (1964)
Michio I, Shinji O, “Decomposition of Solid Residue,” Jpn. Kokai Tokkyo Koho, JP2000-136264 (2000)
Treybig DS, Hock KJ, Kent VA, Dai SA, “A Process for Recovering Toluene Diaamine from Toluene Diisocyanate Distillation Residues,” PCT Patent No. WO 00/68180 (2000)
Kim YC, Lee SB, Yook SH, Choi IY, Lim YM, “A Process for Toluene Diamine Recovery,” Korea Patent No. 10-0383217 (2003)
Nagase Y, Fukuzato R, “Method of and Apparatus for Decomposing Wastes,” U.S. Patent No. 6,255,529 (2001)
Yuk HM, Park JH, Park S, Lee CH, HWAHAK KONGHAK, 41(2), 249 (2003)
Nagase Y, Yamagata M, Kobelco Technology Review, 22, 11 (1999)
Sato O, Arai K, Shirai M, Catal. Today, 111(3-4), 297 (2006)
Lee WY, Park SD, Yeo SD, HWAHAK KONGHAK, 39(2), 257 (2001)
Shanableh A, Water Res., 34, 945 (2000)
Nordquist AF, Pierantiozzi R, “Process for the Disproportionation of Alkylated Aromatic Primary Amines,” U.S. Patent No. 4,935,545 (1990)