Articles & Issues
- Language
- korean
- Conflict of Interest
- In relation to this article, we declare that there is no conflict of interest.
- Publication history
-
Received July 24, 2008
Accepted August 29, 2008
-
This is an Open-Access article distributed under the terms of the Creative Commons Attribution Non-Commercial License (http://creativecommons.org/licenses/bync/3.0) which permits unrestricted non-commercial use, distribution, and reproduction in any medium, provided the original work is properly cited.
Copyright © KIChE. All rights reserved.
All issues
Water Gas Shift Reaction을 위한 Multi-tubular Reactor 모델링 및 모사
Rigorous Modeling and Simulation of Multi-tubular Reactor for Water Gas Shift Reaction
한밭대학교 화학공학과, 305-719 대전시 유성구 덕명동 산 16-1 1포항산업과학연구원 연료전지연구단, 790-600 경북 포항시 남구 효자동 산 32 2포스코 기술연구소 제선연구그룹, 790-785 경북 포항시 남구 괴동동 1
Department of Chemical Engineering, Hanbat National University, San 16-1, Dukmyung-dong, Yuseong-gu, Daejeon 305-719, Korea 1Fuel Cell, Project, San 32 Hyoja-dong, Nam-gu, Pohang, Gyeongbuk 790-600, Korea 2Technical Research Laboratories, Ironmaking Research Group, POSCO, 1 Goedong-dong, Nam-gu, Pohang, Gyeongbuk 790-785, Korea
minoh@hanbat.ac.kr
Korean Chemical Engineering Research, October 2008, 46(5), 931-937(7), NONE Epub 10 November 2008
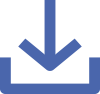
Abstract
공정변수의 변화와 반응기의 성능을 정확하게 예측하기 위하여 Water Gas Shift Reaction(WGSR)을 위한 Multi-Tubular Reactor (MTR)의 상세 multiscale 모델링과 모사를 수행하였다. MTR은 비 균일 고체 촉매로 충진 된 4개의 관형반응기와 냉각을 위해 주변을 싸고 있는 shell side로 구성되어 있다. 유체의 흐름과 반응 kinetics가 반응기 성능에 큰 영향을 주고 있는 점을 고려할 때, Computational Fluid Dynamics (CFD)기법과 공정모델링 기법을 포함한 multiscale 방법론의 채택은 자연스럽고 필수 불가결한 일이다. 345 oC로 관형반응기 부분으로 유입된 반응물은 반응의 결과 390 oC로 45 oC가량 온도가 증가하였으며, CO의 전환율은 0.89에 이르렀다. 쉘 사이드로 190 oC로 유입된 유체는 쉘 출구에서 240 oC로 약 50 oC 가량의 온도 증가를 보였으며 이를 통하여 에너지 절감효과를 가져 올 수 있었으며 높은 전환율을 얻기 위해 반응기 부분의 온도를 적절히 제어할 수 있었다. 모사의 결과는 여러 문헌에 보고된 실험 결과와 매우 근접한 값을 나타내 본 연구를 통해 제시된 모델과 모사의 결과가 정확함을 알 수 있었다.
Rigorous multiscale modelling and simulation of the MTR for WGSR was carried out to accurately predict the behavior of process variables and the reactor performance. The MTR consists of 4 fixed bed tube reactors packed with heterogeneous catalysts, as well as surrounding shell part for the cooling purpose. Considering that fluid flow field and reaction kinetics give a great influence on the reactor performance, employing multiscale methodology encompassing Computational Fluid Dynamics (CFD) and process modeling was natural and, in a sense, inevitable conclusion. Inlet and outlet temperature of the reactant fluid at the tube side was 345 oC and 390 oC, respectively and the CO conversion at the exit of the tube side with these conditions approached to about 0.89. At the shell side, the inlet and outlet temperature of the cooling fluid, which flows counter-currently to tube flow, was 190 oC and 240 oC. From this heat exchange, the energy saving was achieved for the flow at shell side and temperature of the tube side was properly controlled to obtain high CO conversion. The simulation results from this research were accurately comparable to the experimental data from various papers.
Keywords
References
Newsome DS, Catal. Rev.-Sci. Eng., 21, 275 (1980)
Rajasree R, Moharir AS, Comput. Chem. Eng., 24(11), 2493 (2000)
Singh CPP, Saraf DN, Ind. Chem. Process Des. Dev., 16, 313 (1977)
Singh CPP, Saraf DN, Ind. Chem. Process Des. Dev., 19, 393 (1980)
Choi Y, Stenger HG, J. Power Sources, 124(2), 432 (2003)
Ovesen CV, Clausen BS, Hammershoi BS, Steffensen G, Askgaard T, Chorkendorff I, Norskov JK, Rasmussen PB, Stoltze P, Taylor P, J. Catal., 158(1), 170 (1996)
Botes FG, Appl. Catal. A: Gen., 328(2), 237 (2007)
Callaghan C, Fishtik I, Datta R, Surf. Sci., 541, 21 (2003)
Fogler HS, Elements of Chemical Reaction Engineering, 3rded., Prentice Hall, Chapter 14(1999)
Lee UJ, Kim KH, Oh M, Korean J. Chem. Eng., 45, 582 (2007)
Ranade VV, Computational Flow Modeling for Chemical Reactor Engineering, Academic Press, Chapter 13(2002)
Nauman EB, Chemical Reactor Design, Optimization and Scaleup, McGraw-Hill, Chapter 8~9(2002)
Hwang SW, Smith R, Chem. Eng. Sci., 59(20), 4229 (2004)
Hwang SW, Linke P, Smith R, Chem. Eng. Sci., 59(20), 4245 (2004)
Rajasree R, Moharir AS, Comput. Chem. Eng., 24(11), 2493 (2000)
Singh CPP, Saraf DN, Ind. Chem. Process Des. Dev., 16, 313 (1977)
Singh CPP, Saraf DN, Ind. Chem. Process Des. Dev., 19, 393 (1980)
Choi Y, Stenger HG, J. Power Sources, 124(2), 432 (2003)
Ovesen CV, Clausen BS, Hammershoi BS, Steffensen G, Askgaard T, Chorkendorff I, Norskov JK, Rasmussen PB, Stoltze P, Taylor P, J. Catal., 158(1), 170 (1996)
Botes FG, Appl. Catal. A: Gen., 328(2), 237 (2007)
Callaghan C, Fishtik I, Datta R, Surf. Sci., 541, 21 (2003)
Fogler HS, Elements of Chemical Reaction Engineering, 3rded., Prentice Hall, Chapter 14(1999)
Lee UJ, Kim KH, Oh M, Korean J. Chem. Eng., 45, 582 (2007)
Ranade VV, Computational Flow Modeling for Chemical Reactor Engineering, Academic Press, Chapter 13(2002)
Nauman EB, Chemical Reactor Design, Optimization and Scaleup, McGraw-Hill, Chapter 8~9(2002)
Hwang SW, Smith R, Chem. Eng. Sci., 59(20), 4229 (2004)
Hwang SW, Linke P, Smith R, Chem. Eng. Sci., 59(20), 4245 (2004)