Articles & Issues
- Language
- korean
- Conflict of Interest
- In relation to this article, we declare that there is no conflict of interest.
- Publication history
-
Received May 31, 2012
Accepted July 16, 2012
-
This is an Open-Access article distributed under the terms of the Creative Commons Attribution Non-Commercial License (http://creativecommons.org/licenses/bync/3.0) which permits unrestricted non-commercial use, distribution, and reproduction in any medium, provided the original work is properly cited.
Copyright © KIChE. All rights reserved.
All issues
저열량 바이오매스 합성가스의 혼소특성
The Duel Fuel Combustion of Low Calorific Biomass Syngas with Fuel Oil
한국에너지기술연구원 청정연료연구단, 305-343 대전 유성구 장동 71-2 1(주)한별산업, 305-343 대전 유성구 장동 71-2
Clean Fuel Research Department, Korea Institute of Energy Research, 71-2 Jang-dong, Yuseong-gu, Daejeon 305-343, Korea 1Han Byeol Industry Co. Ltd, 71-2 Jang-dong, Yuseong-gu, Daejeon 305-343, Korea
jaegoo@kier.re.kr
Korean Chemical Engineering Research, October 2012, 50(5), 860-865(6), 10.9713/kcer.2012.50.5.860 Epub 2 October 2012
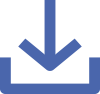
Abstract
바이오매스 합성가스는 저열량 가스이지만 유류를 대체하기 위한 목적으로 공업로, 보일러 등에서 혼소방법으로 이용되고 있다. 혼소버너의 기본구조는 오일버너를 중심부로 하고 저열량 가스 연료를 그 주위로 공급하는 형태로 설계되었다. 본 연구에서는 가스의 균일분산 방법과 가스노즐 각도를 변화시키는 방법을 적용하여 세 종류의 버너를 설계하였다. 연소공기량 증가에 따라 CO 발생량이 감소하였으며, 혼소조건에서 화염으로부터 잔염 발생 원인은 오일버너로부터 미립화 불량인 것으로 나타났다. 혼소조건에서는 가스와 오일연료에 대한 과잉공기 요구량이 서로 다르기 때문에 적절하게 연소공기량을 맞추기가 어려웠지만, 과잉산소 4.7~8.2% 범위에서 안정적인 연소조건 유지가 가능하였다. 본 연구를 통하여 합성가스와 유류의 혼소 이용은 합성가스 성분이 오일보다 연소속도가 빠르게 이루어져 오일버너 미립화를 촉진시켜주고, 오일 단독연소조건보다 CO 배출 농도를 낮게 유지할 수 있음을 알 수 있었다.
Although biomass syngas is very low calorific gas, it is utilized by means of dual fuel combustion technology in the fields of industrial furnace and boiler as a substitute oil technology. The basic structure of duel fuel combustion burner is designed so that low caloric gas fuel is supplied around an oil burner in the middle. In the present study, three types of mixing burners were manufactured to conduct performance experiment. Low caloric gas was evenly distributed around the oil burner and the method of changing the angle of gas nozzle was applied. CO generation decreased according to the increase of the amount of air for combustion. In addition, the shapes and colors of flame changed according to the proportions of gas and oil used. Remained flame after combustion was from the lack of atomization at the exit of oil burner. Although it was difficult to maintain the optimum air ratio due to different required air ratio for oil and syngas, stable combustion was able to maintained within excess oxygen concentration of 4.7~8.2%. From this study, it was shown that the oil atomization at the exit of fuel oil nozzle was promoted by the increased rate of syngas combustion and the CO concentration in flue gas lower than only fuel oil combustion.
Keywords
References
Boocock, eds., “Developments in Thermochemical Biomass Conversion,” 2, Blackie, London (1997)
Higman C, Burgt M, “Gasification,” New York, Elsevier (2003)
Mike S, “A New Standard for Distributed Biomass CHP,” Nexterra Presentation for EPA CHP Partnership, June (2009)
Al-Halbouni A, Rahms H, Grner K, Fredriksson C, “New Burner Technology for Low Grade Biofuels,” GWI Report (2007)
Kim TK, Park J, Cho HC, J. of the Environmental Sciences., 17, 689 (2008)
Al-Halbouni A, Rahms H, Grner K, “An Efficient Combustion Concept for Low Calorific Gases,” ICREPQ'07, Sevilla (2007)
Heating Equipment Management, “Fuel Diversification and Burner System,”, 62 (2006)
IHEA, “Combustion Technology Manual,” (1988)
Kim JJ, Kim CY, Park IS, Kim HJ, Sung DY, Seo YS, “An Experimental Study on the Diffusion Flame with Swirling Flow,” KE-91006B, KIER Report (1991)
Colson G, Peeters F, De Ruyck J, Fuel, 78(11), 1253 (1999)
Cornforth JR, “Combustion Engineering and Gas Utilization, British Gas, 95 (1992)
Francisco RW, Rusa F, Costa M, Catapan RC, Oliveira AAM, “Combustion Characteristics of Gaseous Fuels with Low Calorific Value in a Porous Burner,” Proceedings of the European Combustion Meeting, Vienna (2009)
Higman C, Burgt M, “Gasification,” New York, Elsevier (2003)
Mike S, “A New Standard for Distributed Biomass CHP,” Nexterra Presentation for EPA CHP Partnership, June (2009)
Al-Halbouni A, Rahms H, Grner K, Fredriksson C, “New Burner Technology for Low Grade Biofuels,” GWI Report (2007)
Kim TK, Park J, Cho HC, J. of the Environmental Sciences., 17, 689 (2008)
Al-Halbouni A, Rahms H, Grner K, “An Efficient Combustion Concept for Low Calorific Gases,” ICREPQ'07, Sevilla (2007)
Heating Equipment Management, “Fuel Diversification and Burner System,”, 62 (2006)
IHEA, “Combustion Technology Manual,” (1988)
Kim JJ, Kim CY, Park IS, Kim HJ, Sung DY, Seo YS, “An Experimental Study on the Diffusion Flame with Swirling Flow,” KE-91006B, KIER Report (1991)
Colson G, Peeters F, De Ruyck J, Fuel, 78(11), 1253 (1999)
Cornforth JR, “Combustion Engineering and Gas Utilization, British Gas, 95 (1992)
Francisco RW, Rusa F, Costa M, Catapan RC, Oliveira AAM, “Combustion Characteristics of Gaseous Fuels with Low Calorific Value in a Porous Burner,” Proceedings of the European Combustion Meeting, Vienna (2009)