Articles & Issues
- Language
- korean
- Conflict of Interest
- In relation to this article, we declare that there is no conflict of interest.
- Publication history
-
Received March 30, 2014
Accepted May 2, 2014
-
This is an Open-Access article distributed under the terms of the Creative Commons Attribution Non-Commercial License (http://creativecommons.org/licenses/bync/3.0) which permits unrestricted non-commercial use, distribution, and reproduction in any medium, provided the original work is properly cited.
Copyright © KIChE. All rights reserved.
All issues
동적 모사를 이용한 에탄 분리탑의 플레어 용량 예측에 관한 연구
Study on the Flare Load Estimation of the Deethanizer using Dynamic Simulation
GS건설 플랜트신사업팀, 110-130 서울특별시 종로구 종로 33 그랑서울 1명지대학교 화학공학과, 449-728 경기도 용인시 처인구 명지로 116
Plant New Business Team, GS E&C, GRAN SEOUL, 33 Jong-ro, Jongno-gu, Seoul 110-130, Korea 1Department of Chemical Engineering, Myongji University, 116 Myongji-ro, Cheoin-gu, Yongin, Gyeonggi 449-728, Korea
pktcj81@gmail.com
Korean Chemical Engineering Research, October 2014, 52(5), 613-619(7), 10.9713/kcer.2014.52.5.613 Epub 1 October 2014
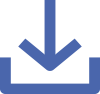
Abstract
화학 공장에서 플레어 시스템은 공장의 안전에 지대한 영향을 주는 아주 중요한 요소이다. 만약, 플레어 시스템이 필요보다 작게 설계 된다면, 위급 상황 발생 시 끔찍한 사고를 유발할 수 있다. 반면, 플레어 시스템이 필요보다 크게 설계하게 된다면 공장을 건설하는데 드는 비용의 증가를 피할 수가 없게 된다. 따라서, 산업계에서는 적절한 플레어 시스템의 설계를 위해 정확한 플레어 배출량을 예측하고자 오랫동안 노력해왔다. 미국석유협회에서는 플레어 배출량 계산을 위한 가이드라인을 제시하였고, 많은 설계 회사들은 정상상태 열 및 물질 수지식을 이용한 방법을 개발하여 플레어 배출량을 예측해 왔다. 하지만, 이러한 방법들은 많은 보수적인 가정들 하에 플레어 배출량을 계산하여 필요보다 크게 설계, 막대한 비용을 초래할 수 있다. 본 연구에서는 기존 방법들이 가지는 문제들을 해결하기 위해 공정제어가 포함된 동적 모사를 통해 플레어 배출량을 계산하는 새로운 절차를 제시하였고, 이 절차에 따라 에탄 분리탑의 배출량을 성공적으로 예측함으로써 절차의 효용성을 증명하였다.
A flare system is a very important system that crucially affects on the process safety in chemical plants. If a flare system is designed too small, it cannot prevent catastrophic accidents of a chemical plant. On the other hand, if a flare system is designed too large, it will waste resources. Therefore, reasonable relief load estimation has been a crucial issue in the industry. American Petroleum Institute (API) suggests basic guidelines for relief load estimation, and a lot of engineering companies have developed their own relief load estimation methods that use an unbalanced heat and material method. However, these methods have to involve lots of conservative assumptions that lead to an overestimation of relief loads. In this study, the new design procedure for a flare system based on dynamic simulation was proposed in order to avoid the overestimation of relief loads. The relief load of a deethanizer process was tested to verify the performance of the proposed design procedure.
References
Jang N, Dan S, Shin D, Lee G, Yoon ES, Korean Chem. Eng. Res., 51(2), 221 (2013)
API, Pressure-relieving and Depressuring Systems, 5th ed., API Publishing Services, Washington, D. C. (2008)
Mofrad SR, Hydrocarb. Process., 87(9), 149 (2008)
Smith D, Burgess J, Hydrocarb. Process., 91(11), 41 (2012)
Cassata JR, Dasgupta S, Gandhi SL, Hydrocarbon Processing, 72, 71 (1993)
Luyben WL, Plantwide dynamic simulators in chemical processing and control, Marcel Dekker, Inc., New York, NY (2002)
Lee CJ, Lim Y, Han C, Korean J. Chem. Eng., 29(4), 444 (2012)
Patel V, Feng J, Dasgupta S, Ramdoss P, Wu J, “Application of Dynamic Simulation in the Design, Operation, and Troubleshooting of Compressor System,” The thirty-sixth turbomachinery symposium, September, Houston, TX (2007)
Patel V, Feng J, Dasgupta S, Kramer J, “Use of Dynamic Simulation in the Design of Ethylene Plants,” The 20th Ethylene Producers' Conference, April, New Orleans, LA (2008)
Singh A, Li K, Lou HH, Hopper JR, Golwala H, Ghumare S, Kelly T, Int. J. Environment and Pollution, 29, 19 (2007)
Xu Q, Yang XT, Liu CW, Li KY, Lou HH, Gossage JL, Ind. Eng. Chem. Res., 48(7), 3505 (2009)
Crwol DA, Louvar JF, Chemical process safety : Fundamentals with applications, 2nd ed., Prentice Hall PTR, Upper Saddle River, NJ (2004)
CCPS, Guidelines for chemical process quantitative risk analysis, 2nd ed., American Institute of Chemical Engineers, New York, NY (2000)
GPSA, Engineering Data Book, 12th ed., Gas Processors Suppliers Association, Tulsa, OK (2004)
API, Pressure-relieving and Depressuring Systems, 5th ed., API Publishing Services, Washington, D. C. (2008)
Mofrad SR, Hydrocarb. Process., 87(9), 149 (2008)
Smith D, Burgess J, Hydrocarb. Process., 91(11), 41 (2012)
Cassata JR, Dasgupta S, Gandhi SL, Hydrocarbon Processing, 72, 71 (1993)
Luyben WL, Plantwide dynamic simulators in chemical processing and control, Marcel Dekker, Inc., New York, NY (2002)
Lee CJ, Lim Y, Han C, Korean J. Chem. Eng., 29(4), 444 (2012)
Patel V, Feng J, Dasgupta S, Ramdoss P, Wu J, “Application of Dynamic Simulation in the Design, Operation, and Troubleshooting of Compressor System,” The thirty-sixth turbomachinery symposium, September, Houston, TX (2007)
Patel V, Feng J, Dasgupta S, Kramer J, “Use of Dynamic Simulation in the Design of Ethylene Plants,” The 20th Ethylene Producers' Conference, April, New Orleans, LA (2008)
Singh A, Li K, Lou HH, Hopper JR, Golwala H, Ghumare S, Kelly T, Int. J. Environment and Pollution, 29, 19 (2007)
Xu Q, Yang XT, Liu CW, Li KY, Lou HH, Gossage JL, Ind. Eng. Chem. Res., 48(7), 3505 (2009)
Crwol DA, Louvar JF, Chemical process safety : Fundamentals with applications, 2nd ed., Prentice Hall PTR, Upper Saddle River, NJ (2004)
CCPS, Guidelines for chemical process quantitative risk analysis, 2nd ed., American Institute of Chemical Engineers, New York, NY (2000)
GPSA, Engineering Data Book, 12th ed., Gas Processors Suppliers Association, Tulsa, OK (2004)