Articles & Issues
- Language
- korean
- Conflict of Interest
- In relation to this article, we declare that there is no conflict of interest.
- Publication history
-
Received December 22, 2016
Accepted March 21, 2017
Available online June 2, 2017
-
This is an Open-Access article distributed under the terms of the Creative Commons Attribution Non-Commercial License (http://creativecommons.org/licenses/bync/3.0) which permits unrestricted non-commercial use, distribution, and reproduction in any medium, provided the original work is properly cited.
Copyright © KIChE. All rights reserved.
All issues
벤치급 CO2 포집공정에서 흡수반응기의 내부구조에 따른 K-계열 고체흡수제의 성능평가
Performance Evaluation of K-based Solid Sorbents Depending on the Internal Structure of the Carbonator in the Bench-scale CO2 Capture Process
Jae-Young Kim
Ho Lim
Je Min Woo
Sung-Ho Jo
Jong-Ho Moon
Seung-Yong Lee
Hyojin Lee
Chang-Keun Yi
Jong-Seop Lee
Byoung-Moo Min
Young Cheol Park†
한국에너지기술연구원 온실가스연구실, 34129 대전광역시 유성구 가정로 152
Greenhouse Gas Research Laboratory, Korea Institute of Energy Research, 152, Gajeong-ro, Yuseong-gu, Daejeon, 34129, Korea
Korean Chemical Engineering Research, June 2017, 55(3), 419-425(7)
https://doi.org/10.9713/kcer.2017.55.3.419
https://doi.org/10.9713/kcer.2017.55.3.419
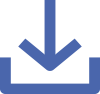
Abstract
본 연구에는 벤치급 건식 CO2 포집 성능평가 장치에서 흡수반응기 내부의 구조와 형태에 따른 K-계열 흡수제 (KEP-CO2P2, 한국전력공사 전력연구원)의 성능특성을 확인하였다. 흡수반응기 혼합영역(mixing-zone)에 구조와 형태가 다르게 제작된 두 종류의 열교환기가 적용되었으며, 각각 CASE 1과 CASE 2로 나뉘어 동일한 조업조건으로 연속운 전을 수행하였다. 연속운전동안 흡수반응 온도는 75~80 °C, 재생반응 온도는 190~200 °C, 그리고 반응기체(CO2) 농도는 12~14 vol%으로 설정하였다. 특히 흡수제의 흡수능 비교를 위해 흡수반응기 혼합영역의 차압을 400~500 mmH2O로 유지하며 운전하였다. 또한 반응 후 채집한 시료는 반응성 비교를 위해 TGA를 이용하여 물성분석을 하였다. CASE 1 실험에서 CO2 제거효율과 동적흡수능은 각각 64.3%, 2.40 wt%으로 산출 되었고, CASE 2 실험에서 CO2 제거효율과 동적흡수능은 각각 81.0%, 4.66 wt%으로 산출되었다. 또한 반응 후 흡수제에 대한 TGA 측정 결과의 무게감량을 이 용하여 흡수제의 동적흡수능을 계산한 결과, CASE 1과 CASE 2 실험에서 반응 후 흡수제의 동적흡수능은 각각 2.51 wt%와 4.89 wt%으로 산출되었다. 결론적으로 동일한 조업조건에서 흡수반응기 내부에 삽입되는 열교환기의 구조와 형태에 따라 흡수제의 성능 차이가 있는 것을 확인하였다.
In this study, the performance characteristics of the K-based sorbents (KEP-CO2P2, KEPCO RI, Korea) has been studied in relation with the heat exchanger structure and shape in a mixing zone of the carbonator in the benchscale dry CO2 capture process. Two types of heat exchangers (different structure and shape) were used in the carbonator as CASE 1 and CASE 2, in which the experiment has been continuously performed under the same operating conditions. During the continuous operation, working temperature of carbonator was 75 to 80 °C, that of regenerator was 190 to 200 °C, and CO2 inlet concentration of the feed gas was 12 to 14 vol%. Especially, to compare the dynamic sorption capacity of sorbents, the differential pressure of the mixing zone in the carbonator was maintained around 400 to 500 mm H2O. Also, solid samples from the carbonator and the regenerator were collected and weight variation of those samples was evaluated by TGA. The CO2 removal efficiency and the dynamic sorption capacity were 64.3% and 2.40 wt%, respectively for CASE 1 while they were 81.0% and 4.66 wt%, respectively for CASE 2. Also, the dynamic sorption capacity of the sorbent in CASE 1 and CASE 2 was 2.51 wt% and 4.89 wt%, respectively, based on the weight loss of the TGA measurement results. Therefore, It was concluded that there could be a difference in the performance characteristics of the same sorbents according to the structure and type of heat exchanger inserted in the carbonator under the same operating conditions.
Keywords
References
Carbon Dioxide Reduction & Sequestration R&D Center “Global Warming, Cause and Measures,” Korea Institute Energy Research(2004).
Wee JH, Kim JL, Song LS, Song BY, Choi KS, "Reduction of Carbon-Dioxide Emission Applying Carbon Capture and Storage (CCS) Technology to Power Generation and Industry Sectors in Korea,” Korean Society of Environmental Engineers, 961-972(2008).
Jeon EC, Sa JH, J. Env. Hlth. Sci., 36(2), 128 (2010)
White CM, Strazisar BR, Granite EJ, Hoffman JS, Pennline HW, J. Air Waste Manage. Assoc., 37, 41 (2013)
Lee SC, Choi BY, Lee TJ, Ryu CK, Soo YS, Kim JC, Catal. Today, 111(3-4), 385 (2006)
Lee SC, Kim JC, Catal. Surv. Asia, 11, 171 (2007)
Lee SC, Chae HJ, Lee SJ, Choi BY, Yi CK, Lee JB, Ryu CK, Kim JC, Environ. Sci. Technol., 42, 2736 (2008)
Lee SC, Chae HJ, Lee SJ, Park YH, Ryu CK, Yi CK, J. Mol. Catal. B-Enzym., 56, 179 (2009)
Lee SC, Chae HJ, Choi BY, Jung SY, Ryu CY, Park JJ, Baek JI, Ryu CK, Kim JC, Korean J. Chem. Eng., 28(2), 480 (2011)
Lee JB, Ryu CK, Baek JI, Lee JH, Eom TH, Kim SH, Ind. Eng. Chem. Res., 47(13), 4465 (2008)
Yi CK, Hong SW, Jo SH, Son JE, Choi JH, Korean Chem. Eng. Res., 43(2), 294 (2005)
Yi CK, Jo SH, Seo Y, Moon KH, Yoo JS, Syud. Surf. Sci. Catal., 159, 501 (2006)
Yi CK, Jo SH, Seo Y, Lee JB, Ryu CK, Int. J. Greenhouse Gas Control, 1(1), 31 (2007)
Yi CK, Jo SH, Seo Y, J. Chem. Eng. Jpn., 41(7), 691 (2008)
Yi CK, Korean Ind. Chem. News, 12(1), 30 (2009)
Yi CK, Korean Chem. Eng. Res., 48(2), 140 (2010)
Kim KC, Kim KY, Park YC, Jo SH, Ryu HJ, Yi CK, Korean Chem. Eng. Res., 48(4), 499 (2010)
Kim KC, Park YC, Jo SH, Yi CK, Korean J. Chem. Eng., 28(10), 1986 (2011)
Park YC, Jo SH, Park KW, Park YS, Yi CK, Korean J. Chem. Eng., 26(3), 874 (2009)
Park YC, Jo SH, Ryu CK, Yi CK, Energy Procedia, 1, 1235 (2009)
Park YC, Jo SH, Ryu CK, Yi CK, Energy Procedia, 4, 1508 (2011)
Kim K, Yang S, Lee JB, Eom TH, Ryu CK, Jo SH, Park YC, Yi CK, Int. J. Greenhouse Gas Control, 9, 347 (2012)
Kim K, Yang S, Lee JB, Eom TH, Ryu CK, Lee HJ, Bae TS, Lee YB, Lee SJ, Korean J. Chem. Eng., 32(4), 677 (2015)
Park YC, Jo SH, Lee DH, Yi CK, Ryu CK, Kim KS, You CH, Park KS, Energy Procedia, 37, 122 (2013)
Park YC, Jo SH, Bae DH, Min BM, Ryu CK, Yi CK, Int. Conference Clean Eng., 1, 2730 (2014)
Park YC, Jo SH, Kyung DH, Kim JY, Yi CK, Ryu CK, Shin MS, Energy Procedia, 63, 2261 (2014)
Park YC, Jo SH, Lee SY, Moon JH, Ryu CK, Lee JB, Yi CK, Korean J. Chem. Eng., 33(1), 73 (2016)
Wee JH, Kim JL, Song LS, Song BY, Choi KS, "Reduction of Carbon-Dioxide Emission Applying Carbon Capture and Storage (CCS) Technology to Power Generation and Industry Sectors in Korea,” Korean Society of Environmental Engineers, 961-972(2008).
Jeon EC, Sa JH, J. Env. Hlth. Sci., 36(2), 128 (2010)
White CM, Strazisar BR, Granite EJ, Hoffman JS, Pennline HW, J. Air Waste Manage. Assoc., 37, 41 (2013)
Lee SC, Choi BY, Lee TJ, Ryu CK, Soo YS, Kim JC, Catal. Today, 111(3-4), 385 (2006)
Lee SC, Kim JC, Catal. Surv. Asia, 11, 171 (2007)
Lee SC, Chae HJ, Lee SJ, Choi BY, Yi CK, Lee JB, Ryu CK, Kim JC, Environ. Sci. Technol., 42, 2736 (2008)
Lee SC, Chae HJ, Lee SJ, Park YH, Ryu CK, Yi CK, J. Mol. Catal. B-Enzym., 56, 179 (2009)
Lee SC, Chae HJ, Choi BY, Jung SY, Ryu CY, Park JJ, Baek JI, Ryu CK, Kim JC, Korean J. Chem. Eng., 28(2), 480 (2011)
Lee JB, Ryu CK, Baek JI, Lee JH, Eom TH, Kim SH, Ind. Eng. Chem. Res., 47(13), 4465 (2008)
Yi CK, Hong SW, Jo SH, Son JE, Choi JH, Korean Chem. Eng. Res., 43(2), 294 (2005)
Yi CK, Jo SH, Seo Y, Moon KH, Yoo JS, Syud. Surf. Sci. Catal., 159, 501 (2006)
Yi CK, Jo SH, Seo Y, Lee JB, Ryu CK, Int. J. Greenhouse Gas Control, 1(1), 31 (2007)
Yi CK, Jo SH, Seo Y, J. Chem. Eng. Jpn., 41(7), 691 (2008)
Yi CK, Korean Ind. Chem. News, 12(1), 30 (2009)
Yi CK, Korean Chem. Eng. Res., 48(2), 140 (2010)
Kim KC, Kim KY, Park YC, Jo SH, Ryu HJ, Yi CK, Korean Chem. Eng. Res., 48(4), 499 (2010)
Kim KC, Park YC, Jo SH, Yi CK, Korean J. Chem. Eng., 28(10), 1986 (2011)
Park YC, Jo SH, Park KW, Park YS, Yi CK, Korean J. Chem. Eng., 26(3), 874 (2009)
Park YC, Jo SH, Ryu CK, Yi CK, Energy Procedia, 1, 1235 (2009)
Park YC, Jo SH, Ryu CK, Yi CK, Energy Procedia, 4, 1508 (2011)
Kim K, Yang S, Lee JB, Eom TH, Ryu CK, Jo SH, Park YC, Yi CK, Int. J. Greenhouse Gas Control, 9, 347 (2012)
Kim K, Yang S, Lee JB, Eom TH, Ryu CK, Lee HJ, Bae TS, Lee YB, Lee SJ, Korean J. Chem. Eng., 32(4), 677 (2015)
Park YC, Jo SH, Lee DH, Yi CK, Ryu CK, Kim KS, You CH, Park KS, Energy Procedia, 37, 122 (2013)
Park YC, Jo SH, Bae DH, Min BM, Ryu CK, Yi CK, Int. Conference Clean Eng., 1, 2730 (2014)
Park YC, Jo SH, Kyung DH, Kim JY, Yi CK, Ryu CK, Shin MS, Energy Procedia, 63, 2261 (2014)
Park YC, Jo SH, Lee SY, Moon JH, Ryu CK, Lee JB, Yi CK, Korean J. Chem. Eng., 33(1), 73 (2016)