Articles & Issues
- Language
- korean
- Conflict of Interest
- In relation to this article, we declare that there is no conflict of interest.
- Publication history
-
Received March 7, 2023
Revised March 24, 2023
Accepted June 13, 2023
-
This is an Open-Access article distributed under the terms of the Creative Commons Attribution Non-Commercial License (http://creativecommons.org/licenses/bync/3.0) which permits unrestricted non-commercial use, distribution, and reproduction in any medium, provided the original work is properly cited.
All issues
바이오매스 순환유동층 보일러의 열교환기 고온 부식 특성
Analysis of High-Temperature Corrosion of Heat Exchanger Tubes in Biomass Circulating Fluidized Bed Boiler
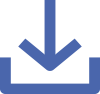
Abstract
본 논문은 상용 바이오매스 발전소 가동 조건에서 열교환기 튜브의 고온 부식 특성 분석 결과를 보고하였다. 3종의
상용 열교환기 튜브(SA213T12, SA213T22, SA213T91) 및 열교환기 튜브의 표면 온도 조절이 가능하도록 자체 설계
된 고온 부식 평가 장치를 사용하였으며, 약 300시간 동안 다양한 온도 및 가동 조건에서 고온 부식 실험을 수행하였
다. 열교환기 튜브 소재에 따른 온도별 고온 부식 특성을 객관적으로 분석하기 위해서 국제표준(ISO 8407)에 입각하
여 부식생성물을 제거 후 고온 부식 실험 전후의 튜브 시편 무게 변화량을 산출하였다. 이를 통해 최종적으로 튜브 시
편의 평균 두께 감육량 및 감육 속도를 도출하였으며, 전자현미경(FE-SEM) 및 에너지분산형 분광분석법(EDS)을 이
요하여 튜브 시편의 표면과 단면의 부식 상태를 분석하였다. 본 연구 결과, 상용 열교환기 소재의 구성 성분 중 크롬
과 니켈의 함량이 증가할수록 소재의 고온 부식 특성이 우수하며, 표면 온도가 증가할수록 고온 부식이 촉진되는 것을
확인하였으며, 열교환 온도 조건에 따른 열교환기 튜브 교체주기를 예측할 수 있었다.
This paper presents the research results of analyzing the high-temperature corrosion characteristics of
three currently commercialized heat exchanger tube materials under actual operating conditions of a biomass power
plant. In order to precisely analyze the high-temperature corrosion characteristics of these materials, a high-temperature
corrosion evaluation device was installed in the power plant equipment, which allows for adjusting the surface temperature of
the heat exchanger tubes. Experiments were conducted for approximately 300 hours under various temperature and
operating conditions. In this study, the commercialized heat exchanger tube materials used were SA213T12, SA213T22,
and SA213T91 alloys. In order to objectively analyze the high-temperature corrosion characteristics of each material, an
international standard-based process to remove corrosion products was applied to obtain the weight change of the specimens, and
the average thickness loss and corrosion rate were derived. Thus, the high-temperature corrosion results for each condition were
quantitatively compared and analyzed. In addition, in order to increase the reliability of the high-temperature corrosion
evaluation method introduced in this study, the surface and cross-sectional corrosion of the specimens were confirmed
by using scanning electron microscopy and energy-dispersive X-ray analysis. Based on these analysis results, it was found that
the corrosion resistance of the commercial heat exchanger materials increases as the content of chrome and nickel in the
composition increases. Additionally, it was found that the corrosion phenomenon is rapidly accelerated as the surface
temperature increases. Finally, the replacement period (lifetime) of the heat exchanger tubes under each condition could
be inferred through this study.
References
2. Antunes, R. A. and de Oliveira, M. C. L., “Corrosion in Biomass Combustion: A Materials Selection Analysis and Its Interaction with Corrosion Mechanisms and Mitigation Strategies,”Corrosion Science, 76, 6-26(2013).
3. Niu, Y. and Tan, H., “Ash-related Issues During Biomass Combustion: Alkali-induced Slagging, Silicate Melt-induced Slagging (ash fusion), Agglomeration, Corrosion, Ash Utilization, and Related Countermeasures,” Progress in Energy and Combustion Science, 52, 1-61(2016).
4. Sandberg, J., Fdhila, R. B., Dahlquist, E. and Avelin, A., “Dynamic Simulation of Fouling in a Circulating Fluidized Biomass-fired Boiler,” Applied Energy, 88(5), 1813-1824(2011).
5. Vainio, E., Kinnunen, H., Laurén, T., Brink, A., Yrjas, P., DeMartini, N. and Hupa, M., “Low-temperature Corrosion in co-combustion of Biomass and Solid Recovered Fuels,” Fuel, 184, 957-965(2016).
6. Lee, S. H., Themelis, N. J. and Castaldi, M. J., “High-temperature Corrosion in Waste-to-energy Boilers,” Journal of Thermal Spray Technology, 16, 104-110(2007).
7. Choi, Y., Jun, H., Shin, J. S., Han, K. H., Bae, D. H., Hwang, B.W., Kim, H. J. and Shun, D., “Effects of Boron Compounds on Decomposition of Chlorides to Control Clinkers Under Solid Refuse Fuel Combustion Conditions,” Energy, 210, 118607(2020).
8. Enestam, S., Bankiewicz, D., Tuiremo, J., Mäkelä, K. and Hupa,M., “Are NaCl and KCl Equally Corrosive on Superheater Materials of Steam Boilers?,” Fuel, 104, 294-306(2013).
9. Imran, M., “Effect of Corrosion on Heat Transfer Through Boiler Tube and Estimating Overheating,” International Journal of Advanced Mechanical Engineering, 4(6), 629-638(2014).
10. Kinnunen, H., Hedman, M., Engblom, M., Lindberg, D., Uusitalo,M., Enestam, S. and Yrjas, P., “The Influence of Flue Gas Temperature on Lead Chloride Induced High Temperature Corrosion,” Fuel, 196, 241-251(2017).
11. Lindberg, D., Backman, R., Chartrand, P. and Hupa, M.,“Towards a Comprehensive Thermodynamic Database for Ashforming Elements in Biomass and Waste Combustion - Current Situation and Future Developments,” Fuel Processing Technology, 105, 129-141(2013).
12. Skrifvars, B. J., Backman, R., Hupa, M., Salmenoja, K. and Vakkilainen, E., “Corrosion of Superheater Steel Materials Under Alkali Salt Deposits Part 1: The Effect of Salt Deposit Composition and Temperature,” Corrosion Science, 50(5), 1274-1282(2008).
13. Skrifvars, B. J., Westén-Karlsson, M., Hupa, M. and Salmenoja,K., “Corrosion of Super-heater Steel Materials Under Alkali Salt Deposits. Part 2: SEM Analyses of Different Steel Materials,”Corrosion Science, 52(3), 1011-1019(2010).
14. Viklund, P., Hjörnhede, A., Henderson, P., Stålenheim, A. and Pettersson, R., “Corrosion of Superheater Materials in a Wasteto-energy Plant,” Fuel Processing Technology, 105, 106-112(2013).
15. Xin, Y. A. N. G., HUANG, J. J., FANG, Y. T. and Yang, W. A. N.G., “Slagging Characteristics of Fly Ash from Anthracite Gasification in Fluidized Bed,” Journal of Fuel Chemistry and Technology, 41(1), 1-8(2013).
16. Bang, J., Kim, Y., Kim, S. R., Shin, D., Cho, K. and Kwon, W.,“High Temperature Corrosion Properties of Heating Surface in Waste-to-energy Boiler Tube,” J. Korea Soc Waste Manag, 34,27-33(2017).
17. Chatha, S. S., Sidhu, H. S. and Sidhu, B. S., “High Temperature Hot Corrosion Behaviour of NiCr and Cr3C2–NiCr Coatings on
T91 Boiler Steel in An Aggressive Environment at 750 C,” Surface and Coatings Technology, 206(19-20), 3839-3850(2012).
18. Fantozzi, D., Matikainen, V., Uusitalo, M., Koivuluoto, H. and Vuoristo, P., “Chlorine-induced High Temperature Corrosion of Inconel 625 Sprayed Coatings Deposited with Different Thermal Spray Techniques,” Surface and Coatings Technology, 318,233-243(2017).
19. Okoro, S. C., Montgomery, M., Frandsen, F. J. and Pantleon, K.,“Influence of Preoxidation on High Temperature Corrosion of a Ni-based Alloy Under Conditions Relevant to Biomass Firing,”Surface and Coatings Technology, 319, 76-87(2017).
20. Oksa, M., Auerkari, P., Salonen, J. and Varis, T., “Nickel-based HVOF Coatings Promoting High Temperature Corrosion Resistance of Biomass-fired Power Plant Boilers,” Fuel Processing Technology, 125, 236-245(2014).
21. Oksa, M., Tuurna, S. and Varis, T., “Increased Lifetime for Biomass and Waste to Energy Power Plant Boilers with HVOF Coatings:High Temperature Corrosion Testing Under Chlorine-containing Molten Salt,” Journal of Thermal Spray Technology, 22, 783-796(2013).
22. Shukla, V. N., Jayaganthan, R. and Tewari, V. K., “Degradation Behavior of HVOF-sprayed Cr3C2-25% NiCr Cermet Coatings Exposed to High Temperature Environment,” Materials Today:Proceedings, 2(4-5), 1805-1813(2015).
23. Varis, T., Bankiewicz, D., Yrjas, P., Oksa, M., Suhonen, T., Tuurna,S., Ruusuvuori K. and Holmström, S., “High Temperature Corrosion of Thermally Sprayed NiCr and FeCr Coatings Covered with a KCl–K2SO4 Salt Mixture,” Surface and Coatings Technology, 265, 235-243(2015).
24. Zhou, W., Zhou, K., Deng, C., Zeng, K. and Li, Y., “Hot Corrosion Behaviour of HVOF-sprayed Cr3C2-NiCrMoNbAl Coating,” Surface and Coatings Technology, 309, 849-859(2017).
25. Dudziak, T., Hussain, T., Simms, N. J., Syed, A. U. and Oakey,J. E., “Fireside Corrosion Degradation of Ferritic Alloys at 600 C in Oxy-fired Conditions,” Corrosion Science, 79, 184-191(2014).