Articles & Issues
- Language
- korean
- Conflict of Interest
- In relation to this article, we declare that there is no conflict of interest.
- Publication history
-
Received November 5, 2023
Revised December 12, 2023
Accepted January 19, 2024
-
This is an Open-Access article distributed under the terms of the Creative Commons Attribution Non-Commercial License (http://creativecommons.org/licenses/bync/3.0) which permits unrestricted non-commercial use, distribution, and reproduction in any medium, provided the original work is properly cited.
All issues
비정상 작업에서 발생한 중대산업사고 분석을 통한 FRAM의 PSM 활용 방안에 관한 연구
A Study on the Application of FRAM to PSM through the Analysis of Serious Industrial Accident in Non-routine Work
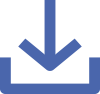
Abstract
복잡한 화학공정을 관리하기 위한 목적으로 도입된 공정안전관리(PSM: process safety management)제도는 그간 화
학사고 예방에 기여해 왔으나, 최근에는 그 한계를 드러내고 있다. 최근 중대산업사고가 증가하고 있으며 특히 2020년
이후 비정상 작업에서 중대산업사고가 급증하였다. 효과적인 PSM 운영 방안이 필요한 시점이다. 본 연구에서는 비선
형적이고 복잡한 상호작용을 모형화하여 인적오류 및 사고 발생 과정을 이해하고 예측하는데 유용한 기법인 기능공명
분석기법(FRAM: Functional Resonance Analysis Method)을 활용하여 비정상 작업에서 발생한 사고 사례를 분석하고
나아가 일반적인 PSM 비정상 작업 수행 과정에 대한 분석을 수행함으로써, PSM 운영 과정에서 FRAM이 효과적으
로 활용될 수 있음을 검토하였다.
PSM(process safety management), introduced for the purpose of managing complex chemical processes, has contributed to the prevention of chemical accidents, but has recently revealed its limitations. Recently, major industrial accidents have increased, and in particular, Serious Industrial Accidents have increased rapidly in non-routine works since 2020. It is time for an effective PSM operation plan. This study examined that FRAM can be effectively used in the PSM operation process by using FRAM (Functional Resonance Analysis Method), a useful technique for understanding and predicting human error and accident occurrence processes by modeling nonlinear and complex interactions, to analyze accident cases that occurred in non-routine works, and to further analyze the process of performing general PSM non-routine works.
References
Assessment in Process Safety Management (PSM) System,”
Journal of the Korean Society of Safety, 31(4), 27-34(2016).
2. Jang, Namjin, et al. “The Role of Process Systems Engineering
for Sustainability in the Chemical Industries,” Korean Chemical
Engineering Research 51(2), 221-225(2013).
3. In Jae Shin, “The Effective Control of Major Industrial Accidents
by the Major Industrial Accident Prevention Centers (MAPC)
Through the Process Safety Management (PSM) Grading System
in Korea,” Journal of Loss Prevention in the Process Industries,
26(4), 803-814(2013).
4. Jung, J.-W., Safety management 4th, GyoMoonSa. 61(2023).
5. Rasmussen, Jens., “Risk Management in a Dynamic Society: a
Modelling Problem,” Safety Science, 27(2-3), 183-213(1997).
6. Hollnagel, Erik and Orjan Goteman, “The Functional Resonance
Accident Model,” Proceedings of Cognitive System Engineering
in Process Plant 2004, 155-161(2004).
7. Patriarca, Riccardo, Johan Bergström, and Giulio Di Gravio.,
“Defining the Functional Resonance Analysis Space: Combining
Abstraction Hierarchy and FRAM,” Reliability Engineering &
System Safety, 165, 34-46(2017).
8. Clay-Williams, Robyn, Jeanette Hounsgaard, and Erik Hollnagel.,
“Where the Rubber Meets the Road: Using FRAM to Align
Work-as-imagined with Work-as-done When Implementing Clinical
Guidelines,” Implementation Science, 10(1), 1-8(2015).
9. França, Josué Eduardo Maia, et al., “Analyzing Organizational
Gaps in Process Accidents with FRAM: The Case of the Imperial
Sugar refinery explosion (2008),” 9th CCPS Latin American Conference
on Process Safety 2022, 394-405(2022).
10. Kim, Y. S. and Parkm, D. J., “A Development of Facility Web Program
for Small and Medium-Sized PSM Workplaces,” Korean
Chem. Eng. Res., 60(3), 334-346(2022).
11. Koo, C.-C., Seo, D.-H. and Kim, T.-H., “Chemical Plant Explosion
Accident (cause) Analysis Using AcciMap and FRAM,” Fire
Science and Engineering, 35(5), 59-65(2021).
12. Seo, D.-H., Choi, Y.-R. and Han, O.-S., “Analysis of a Fire Accident
during a Batch Reactor Cleaning with AcciMap, STAMP and
FRAM,” Journal of the Korean Society of Safety, 36(4), 62-70
(2021).
13. Seol, M.-S., “A Study on Implications for the Prevention of Major
Industrial Accidents Based on the Causes and Statistic of Major
Industrial Accidents,” Korean Journal of Hazardous Materials
10(2), 97-106(2022).
14. OSHA., Process Safety Management OSHA 3132., 2000(Reprinted)).
15. Kang, M.-J., Lee, Y.-S. and Kwon, H.-M., “A Study on the Development
of Safety Performance Index in Chemical Industry,”
Journal of the Korean Society of Safety, 23(6), 57-61(2008).
16. Dohyung Kee, “Review and Comparison of Systemic Accident
Analysis Techniques based on Literature Survey,” Journal of the Ergonomics Society of Korea, 40(1), 55-63(2021).
17. Hollnagel Erik., Safety-I and safety-II: the past and future of
safety management. CRC press(2018).
18. Ham, D.-H., “Safety-II and Resilience Engineering in a Nutshell:
An Introductory Guide to Their Concepts and Methods,”
Safety and Health at Work, 12(1), 10-19(2021).
19. Patriarca, Riccardo, et al. “Framing the FRAM: A Literature Review
on the Functional Resonance Analysis Method,” Safety Science
129, 104827(2020).
20. Choi, E.-B. and Ham, D.-H., “A FRAM-Based Systemic Investigation
of a Rail Accident involving Human Errors,” Journal of
the Korea Safety Management & Science, 22(1), 23-32(2020).
21. Furniss, Dominic, Paul Curzon, and Ann Blandford. “Using FRAM
Beyond Safety: a Case Study to Explore How Sociotechnical
Systems Can Flourish or Stall,” Theoretical Issues in Ergonomics
Science 17(5-6), 507-532(2016).
22. Hollnagel, Erik., FRAM: the functional resonance analysis
method: modelling complex socio-technical systems. Crc Press,
(2017).
23. Seo, D.-H., Han, O.-S. and Cho, Y.-R., “A Study on Systematic
Cause Analysis of Fire and Explosion Accident Cases in Chemical
Plants,” OSHRI, KOSHA. 33-43(2020).
24. França, Josué Eduardo Maia, and Erik Hollnagel. “Recognition
and Analysis of Human Factors and Non-technical Skills Using
the Functional Resonance Analysis Method-FRAM,” Anais do
Congresso Internacional de Conhecimento e Inovação–ciki. 1(1),
(2019).
25. Yoon, W. C. and Yang, J. Y., “A Study for Change the Tional
Safety and Health Paradigm,” OSHRI, KOSHA. 67-80(2019).
26. Underwood, Peter, and Patrick Waterson. “A Critical Review of
the STAMP, FRAM and Accimap Systemic Accident Analysis
Models,” Advances in Human Aspects of Road and Rail Transportation
January 2016, 385-394(2012).
27. Branford, Kate, Andrew Hopkins, and Neelam Naikar. “Guidelines
for AcciMap Analysis,” Learning from high reliability organisations.
CCH Australia Ltd(2009).
28. Salmon, Paul, et al. “Systems-based Accident Analysis in the
Led Outdoor Activity Domain: Application and Evaluation of a
Risk Management Framework,” Ergonomics 53(8), 927-939((2010)).
29. Leveson, Nancy. “A New Accident Model for Engineering Safer
Systems,” Safety Science 42(4), 237-270(2004).
30. Salmon, Paul M., Miranda Cornelissen, and Margaret J. Trotter.
“Systems-based Accident Analysis Methods: A Comparison of
Accimap, HFACS, and STAMP,”Safety Science 50(4), 1158-1170
(2012).
31. KOSHA., Example process safety report preparation(2020).