Overall
- Language
- korean
- Conflict of Interest
- In relation to this article, we declare that there is no conflict of interest.
- Publication history
-
Received December 7, 2023
Revised April 30, 2024
Accepted May 22, 2024
Available online August 1, 2024
-
This is an Open-Access article distributed under the terms of the Creative Commons Attribution Non-Commercial License (http://creativecommons.org/licenses/bync/3.0) which permits unrestricted non-commercial use, distribution, and reproduction in any medium, provided the original work is properly cited.
Most Cited
머신 러닝을 이용한 밸브 사이즈 및 종류 예측 모델 개발
Data-driven Modeling for Valve Size and Type Prediction Using Machine Learning
https://doi.org/10.9713/kcer.2024.62.3.214
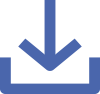
Abstract
밸브는 유량과 압력 조절 등의 중요한 역할을 수행하며, 적절한 밸브 사이즈와 유형 선택이 필요하다. Engineering
Procurement Construction (EPC) 산업에선 밸브 사이즈 계수(Cv)의 수식적 계산을 바탕으로 사이즈와 유형을 선정해
왔으나 이러한 방식은 전문가의 많은 시간과 비용이 요구되어 비효율적이다. 본 연구는 이를 해결하기위해 머신 러닝
기법을 이용한 밸브 사이즈 및 유형 예측 모델을 개발하였다. Artificial neural network (ANN), Random Forest, XGBoost,
Catboost의 알고리즘을 적용하여 모델들을 개발하였으며, 평가 지표로는 사이즈 예측에는 Normalized root mean squared
error (NRMSE)와 R2를, 종류 예측에는 F1 score를 적용하였다. 또한, 유체 상에 따른 영향을 확인하고자 유체 전체, 액체,
기체, 스팀의 4개의 데이터 세트로 사례 연구를 진행하였다. 연구 결과, 사이즈의 경우 전체, 액체, 기체에선 Catboost(R2
기준, 전체: 0.99216, 액체: 0.98602, 기체: 0.99300. NRMSE 기준, 전체: 0.04072, 액체: 0.04886, 기체: 0.03619)가, 스팀에
선 Random Forest가(R2: 0.99028, NRMSE: 0.03493) 가장 뛰어난 모델임을 확인하였다. 종류의 경우 Catboost가 모
든 데이터에서 가장 높은 성과를 제시하였다(F1 score 기준, 전체: 0.95766, 액체: 0.96264, 기체: 0.95770, 스팀: 1.0000).
본 연구에서 제안한 모델들을 적용할 경우, 주어진 조건에 따른 밸브 선택을 도와 의사결정 속도를 높여줄 것으로 기
대된다.
Valves play an essential role in a chemical plant such as regulating fluid flow and pressure. Therefore,
optimal selection of the valve size and type is essential task. Valve size and type have been selected based on theoretical
formulas about calculating valve sizing coefficient (Cv). However, this approach has limitations such as requiring expert
knowledge and consuming substantial time and costs. Herein, this study developed a model for predicting valve sizes
and types using machine learning. We developed models using four algorithms: ANN, Random Forest, XGBoost, and
Catboost and model performances were evaluated using NRMSE & R2 score for size prediction and F1 score for type
prediction. Additionally, a case study was conducted to explore the impact of phases on valve selection, using four
datasets: total fluids, liquids, gases, and steam. As a result of the study, for valve size prediction, total fluid, liquid, and gas
dataset demonstrated the best performance with Catboost (Based on R2, total: 0.99216, liquid: 0.98602, gas: 0.99300.
Based on NRMSE, total: 0.04072, liquid: 0.04886, gas: 0.03619) and steam dataset showed the best performance with RandomForest (R2: 0.99028, NRMSE: 0.03493). For valve type prediction, Catboost outperformed all datasets with the highest F1 scores (total: 0.95766, liquids: 0.96264, gases: 0.95770, steam: 1.0000). In Engineering Procurement Construction industry, the proposed fluid-specific machine learning-based model is expected to guide the selection of suitable valves based on given process conditions and facilitate faster decision-making.
References
10(3), 141-152(1972).
2. Driskell, Les. Control valve selection and sizing. 1st ed. North
Carolina: Creative Services Inc; 1983.
3. IEC 60534-2-1 Mod: flow equations for sizing control valves,
Switzerland, International Electro-technical Commission.
4. ISA75.01, Control Valve Sizing Equations, International Society
of Automation.
5. Grace, A. and Frawley, P., “Experimental Parametric Equation
for the Prediction of Valve Coefficient (Cv) for Choke Valve
Trims,” International Journal of Pressure Vessels and Piping,
88(2–3), 109-118(2011).
6. Long, C. and Guan, J., “A Method for Determining Valve Coefficient
and Resistance Coefficient for Predicting Gas Flowrate,”Experimental Thermal and Fluid Science, 35(6), 1162-1168(2011).
7. Zhou, X.-M., Wang, Z.-K., Zhang, Y.-F., “A Simple Method for
High-precision Evaluation of Valve Flow Coefficient by Computational
Fluid Dynamics Simulation,” Advances in Mechanical
Engineering, 9(7), 1-7(2017).
8. Lisowski, E. and Filo, G., “Analysis of a Proportional Control
Valve Flow Coefficient with the Usage of a CFD Method,” 53,
Part B, 269-278(2017).
9. Valdés, J. R., Rodríguez, J. M., Saumell, J, Pütz, T., “A Methodology
for the Parametric Modelling of the Flow Coefficients
and Flow Rate in Hydraulic Valves,” Energy Conversion and
Management, 88, 598-611(2014).
10. Nguyen, Q. K. and Jung, K. H., “Experimental Study on Pressure
Characteristics and Flow Coefficient of Butterfly Valve,” International
Journal of Naval Architecture and Ocean Engineering,
15, (2023).
11. Al-Zaidi, B. M. and Ismaeel, A. J., “Effect of Hydraulic Characteristics
on Fluid Transients Analysis under Different Types of
Control Valves,” Journal of Ecological Engineering, 23(12),
111-123(2022).
12. Fu, W.-S. and Ger, J.-S., “A Concise Method for Determining a
Valve Flow Coefficient of a Valve Under Compressible Gas Flow,”
Experimental Thermal and Fluid Science, 18, 307-313(1999).
13. Boccardi, G., Bubbico, R. and Celata, G. P., “Geometry Influence
on Safety Valves Sizing in Two-phase Flow,” Journal of Loss
Prevention in the Process Industries, 21(1), 66-73(2008).
14. Mahalleh, VBS, YOLO-Based Valve Type Recognition and Localization,
2019 IEEE 6th International Conference On Industrial Engineering
and Applications (Iciea), 37-40(2019).
15. Hlubek, N. and Baumann, M., Sebastian Heinze Florian Ostermaier,
Using Machine Learning for Diaphragm Prediction in
Solenoid Valves, IEEE 27th International Conference on Emerging
Technologies and Factory Automation (ETFA).
16. Roh, J., Park, H., Kwon, H., Joo, C., Moon, I., Cho, H., Ro, I. and
Kim, J., “Interpretable Machine Learning Framework for Catalyst
Performance Prediction and Validation with Dry Reforming of
Methane,” Applied Catalysis B: Environmental, 343, 123454(2024).
17. Roh, J., Oh, S., Lee, D., Joo, C., Park, J., Moon, I., Ro, I., Kim,
J., “Hybrid Quantum Neural Network Model with Catalyst
Experimental Validation: Application for the Dry Reforming of
Methane,” ACS Sustainable Chemistry & Engineering, 12(10),
4121-4131(2024).
18. Kwon, H., Oh, K. C., Choi, Y., Chung, Y. G. and Kim, J.,
“Development and Application of Machine Learning-based Prediction
Model for Distillation Column,” International Journal of
Intelligent Systems, 36(5), 1970-1997(2021).
19. Jeong, S., Joo, C., Lim, J., Cho, H., Lim, S. and Kim, J., “A Novel
Graph-based Missing Values Imputation Method for Industrial
Lubricant Data,” Computers in Industry, 150, 103937(2023).
20. Lee, J., Hong, S., Kim, J. and Moon, I., “Machine Learning-based
Energy Optimization for on-site SMR Hydrogen Production,”
Energy Conversion and Management, 244(15), 114438(2021).
21. Lim, J., Jeong, S. and Kim, J., “Deep Neural Network-based
Optimal Selection and Blending Ratio of Waste Seashells as an
Alternative to High-grade Limestone Depletion for SOX Capture
and Utilization,” Chemical Engineering Journal, 431, Part 3,
133244(2022).
22. Joo, C., Park, H. and Kim, J., “Development of Physical Property
Prediction Models for Polypropylene Composites with Optimizing
Random Forest Hyperparameters,” International Journal of Intelligent
Systems, 37(6), 3189-3771(2022).
23. Joo, C., Park, H., Kwon, H. and Kim, J., “Machine Learning
Approach to Predict Physical Properties of Polypropylene Composites:
Application of MLR, DNN, and Random Forest to Industrial
Data,” Polymers, 14(17), 3500(2022).
24. Joo, C., Park, H. and Kim, J., “Data-driven Modeling for Physical
Property Prediction of Polypropylene Composites Using
Artificial Neural Network and Principal Component Analysis,”
Computer Aided Chemical Engineering, 51, 1369-1374(2022).
25. Lee, Y., Choi, Y., Cho, H. and Kim, J., “Prediction of Distillation
Column Temperature Using Machine Learning and Data Preprocessing,”
Korean Chem. Eng. Res., 59(2), 191-199(2021).
26. Joo, C., Park, H., Lim, J., Cho, H. and Kim, J., “Machine Learning-
based Heat Deflection Temperature Prediction and Effect
Analysis in Polypropylene Composites Using Catboost and Shapley
Additive Explanations,” Engineering Applications of Artificial
Intelligence, 126, Part A, 1801-1806(2022).
27. Chen, T. and Guestrin, C., XGBoost: A Scalable Tree Boosting
System, 22nd ACM SIGKDD International Conference on Knowledge
Discovery and Data Mining (KDD), 785-794(2016).
28. Dorogush, A. V., Ershov, V. and Gulin, A., “CatBoost: Gradient
Boosting with Categorical Features Support,”Workshop on ML
Systems at NIPS 2017.