Overall
- Language
- korean
- Conflict of Interest
- In relation to this article, we declare that there is no conflict of interest.
- Publication history
-
Received March 22, 2024
Revised July 8, 2024
Accepted July 29, 2024
Available online November 1, 2024
-
This is an Open-Access article distributed under the terms of the Creative Commons Attribution Non-Commercial License (http://creativecommons.org/licenses/bync/3.0) which permits unrestricted non-commercial use, distribution, and reproduction in any medium, provided the original work is properly cited.
Most Cited
유연탄 분진특성분석을 통한 폭발 위험성 평가
Explosion Risk Assessment by Analysis of the Dust Characteristics of Bituminous Coal
https://doi.org/10.9713/kcer.2024.62.4.327
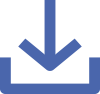
Abstract
폭발 가능성에 영향을 미치는 다양한 특성을 분석하여 석탄 분진 폭발과 관련된 위험성을 조사했다. 석탄화력발전
소에서 가장 많은 폭발이 발생한 이송공정의 두 지역에서 시료를 직접 채취하여 실험에 영향을 미칠 수 있는 조성비
와 평균 입경을 고려했다. 실험항목으로는 폭발에 영향을 미치는 폭발강도, 입자크기와 분포, 수분함량, 분진농도, 최
소점화에너지, 최소점화온도, 산소농도를 평가했다. 그 결과 폭발강도는 시료 A에서 분진농도 500 g/m3에서 최대 폭발
압력이 7.1 bar, 최대 폭발압력 증가율은 366 bar/s로 나타났다. 분진 입경과 입자크기 분포에서 시료 A는 평균 직경이
35 μm(D 50%)로 시료 B보다 작았다. 수분함량은 시료 A에서 5.7%로 시료 B에서 2.5%보다 2배 이상 높았다. 최소
폭발농도는 시료 A에서 400 g/m3로 시료 B에서 2,000 g/m3보다 낮아 위험성을 가지고 있었다. 두 시료 모두 1,000 mJ
에서 폭발하지 않았기 때문에 최소 에너지가 500 mJ 이상이면 유사한 선행 연구에 비해 점화에 대한 민감도가 낮은
분진으로 간주할 수 있을 것으로 판단된다. 최소점화온도는 시료 A에서 532℃, 시료 B에서 634℃로 시료 A가 시료 B
보다 더 위험했다. 한계 산소농도는 두 시료 모두 18.0%로 대기 중 폭발 위험성이 일정하게 존재하는 것으로 판단된다.
The risks associated with coal dust explosion were investigated by analyzing various characteristics
affecting the possibility of explosion. Samples were collected directly from two regions of the transfer process where the
most explosions occurred in coal-fired power plants, and the composition ratio and average particle diameter that could
affect the experiment were considered. As experimental items, explosion intensity, particle size and distribution, moisture
content, dust concentration, minimum ignition energy, minimum ignition temperature, and oxygen concentration that affect the
explosion were evaluated. As a result, the explosion intensity was found to have a maximum explosion pressure of 7.1
bar at a dust concentration of 500 g/m3 in sample A, and the maximum explosion pressure increase rate was 366 bar/s. In
terms of dust particle diameter and particle size distribution, sample A had an average diameter of 35 μm (D 50%),
which was smaller than sample B. The moisture content was 5.7% in sample A, which was more than twice as high as
2.5% in sample B. The minimum explosion concentration was 400 g/m3 in sample A, which was lower than 2,000 g/m3
in sample B, so it had a risk. Since neither sample exploded at 1,000 mJ, it is judged that if the minimum energy is 500 mJ or
higher, it can be regarded as dust with a low sensitivity to ignition compared to similar previous studies. The minimum
ignition temperature was 532℃ in sample A and 634℃ in sample B, so sample A was more dangerous than sample B.
The marginal oxygen concentration was 18.0% in both samples, so it is judged that there is a constant risk of explosion
in the atmosphere.
References
Prevention and Mitigation: An Overview,” Journal of Chemical
Health & Safety, 17(1), 15-28(2010).
2. Han, O. S. and Lee, K. W., “Influence of the Magnesium Content
on the Explosion Properties of Mg-Al Alloy Dusts,” Journal of
the Korean Institute of Gas, 16(6), 1-6(2012).
3. Abbasi, T. and Abbasi, S. A., “Dust Explosions–Cases, Causes,
Consequences, and Control,” Journal of Hazardous Materials,
140(1-2), 7-44(2007).
4. Li, Q., Lin, B., Dai, H. and Zhao, S., “Explosion Characteristics
of H2/CH4/air and CH4/coal Dust/air Mixtures,” Powder Technology,
229, 222-228(2012).
5. Park, C. S. and Kim, C. O., “Risk Assessment of Explosion of
Mixed Dust Generated in Semiconductor Manufacturing. The
Transactions of the Korean Institute of Electrical Engineers,
67(3), 474-478(2018).
6. Lee, J. Y., Lee, K. W., Park, S. Y. and Han, I. S., “Explosion Hazard
Assessment of Pharmaceutical Raw Materials Powders. Korean
Chemical Engineering Research, 55(5), 600-608(2017).
7. Ebadat, V., “Dust Explosion Hazard Assessment,” Journal of Loss
Prevention in the Process Industries, 23(6), 907-912(2010).
8. Cao, W., Huang, L., Zhang, J., Xu, S., Qiu, S., Pan, F., “Research
on Characteristic Parameters of Coal-dust Explosion,” Procedia
Engineering, 45, 442-447(2012).
9. Han, I. S., Lee, K. W. and Choi, Y. R., Dust Explosion Characteristics
of Multi-Walled Carbon Nano Tube,” Korean Chemical
Engineering Research, 55(1), 40-47(2017).
10. Sun, K. J., Study on the Thermal Characteristic Comparison of
Fire. Explosion Hazard of Fugitive Dust Generated in the Manufacturing
Process. Journal of the Society of Disaster Information,
10(1), 71-83(2014).
11. Ma, B. C., A Study on Improvement of Fire and Explosion Risk
of Flammable Solid. Doctoral thesis. Department of Chemical
Engineering, Chonnam National University(2017).
12. ASTM E1226-19, Standard Test Method for Explosibility of
Dust Clouds(2020).
13. ASTM E2019-03, Standard Test Method for Minimum Ignition
Energy of a Dust Cloud in Air(2019).
14. ASTM E1491-06, Standard Test Method for Minimum Autoignition
Temperature of Dust Clouds(2019).
15. Joseph, G. and Team, C. H. I., “Combustible Dusts: A Serious
Industrial Hazard,” Journal of Hazardous Materials, 142(3), 589-
591(2007).
16. ASTM E2550-11, Standard Test Method for Thermal Stability
by Thermogravimetry(2011).
17. ASTM E537-12, Standard Test Method for The Thermal Stability
of Chemicals by Differential Scanning Calorimetry(2012).
18. Mao, Z., Zhu, H., Zhao, X., Sun, J. and Wang, Q., “Experimental
Study on Characteristic Parameters of Coal Spontaneous Combustion,”
Procedia Engineering, 62, 1081-1086(2013).
19. Jung, W. J. and Nagai, H., “Explosion Characteristics of Magnesium
Dust according to the Variation of Particle Size,” Journal of
the Korean Society of Hazard Mitigation, 13(2), 203-208(2013).
20. Liu, H., Chen, Z., Chen, B., Xiao, X. and Wang, X., “Studies on the
Temperature Distribution of Steel Plates with Different Paints Under
Solar Radiation. Applied Thermal Engineering, 71(1), 342-354
(2014).
21. Ou-Sup HAN, “Study on Prevention and Improvement of Fires
and Explosions in Dust Collection Process,” Chemicals Safety &
Health Research Center, Occupational Safety and Health Research
Institute, KOSHA(2018).
22. Zhanli Mao, et al., “Experimental Study on Characteristic Parameters
of Coal Spontaneous Combustion,” Procedia Engineering, 62,
1081-1086(2013).
23. Yuan, Z., Khakzad, N., Khan, F. and Amyotte, P., “Dust Explosions:
A Threat to the Process Industries,” Process Safety and
Environmental Protection, 98, 57-71(2015).
24. Zhong, S. and Wang, Z., “Coal Pulverization System: Explosion
Prevention and Process Control,” Measurement. Control, 42(3),
81-83(2009).