Articles & Issues
- Language
- english
- Conflict of Interest
- In relation to this article, we declare that there is no conflict of interest.
- Publication history
-
Received August 2, 2017
Accepted September 14, 2017
-
This is an Open-Access article distributed under the terms of the Creative Commons Attribution Non-Commercial License (http://creativecommons.org/licenses/bync/3.0) which permits unrestricted non-commercial use, distribution, and reproduction in any medium, provided the original work is properly cited.
Copyright © KIChE. All rights reserved.
All issues
A Simple Method to Make the Quadruple Tank System Near Linear
Jietae Lee†
Inhyun Kyoung
Jea Pil Heo
YoungSu Park
Yugyeong Lim
Dong Hyun Kim
Yongjeh Lee1
Dae Ryook Yang1
Department of Chemical Engineering, Kyungpook National University, 80, Daehak-ro, Buk-gu, Daegu, 41566, Korea 1Department of Chemical and Biological Engineering, Korea University, 145, Anam-ro, Seongbuk-gu, Seoul, 02841, Korea
jtlee@knu.ac.kr
Korean Chemical Engineering Research, December 2017, 55(6), 767-770(4), 10.9713/kcer.2017.55.6.767 Epub 5 December 2017
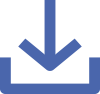
Abstract
Quadruple tank liquid level systems are popular in testing multivariable control systems for multivariable processes with positive or negative zeros. The liquid level system is nonlinear and it will help to illustrate the robustness of control systems. However, due to nonlinearity, it can be cumbersome to obtain process parameters for testing linear control systems. Perturbation sizes are limited for valid linearized process models, requiring level sensors with high precision. A simple method where the outlet orifice is replaced to a long tube is proposed here. The effluent flow rate becomes proportional to the liquid level due to the friction loss of long tube and the liquid level system shows near linear dynamics. It is applied to the quadruple tank system for easier experiments.
Keywords
References
Astrom KJ, Ostberg AB, IEEE Control Systems Magazine, 6(5), 37 (1986)
Edgar TF, Ogunnaike BA, Downs JJ, Muske KR, Bequette BW, Comp. Chem. Eng., 30(10-12), 1749 (2006)
Johansson KH, IEEE Trans. Control Systems Technology, 8(3), 456 (2000)
Abdullah A, Zribi M, Int. J. Comput. Commun., 7(4), 594 (2012)
Alavi SM, Khaki-Sedigh A, Labibi B, Hayes MJ, IET Control Theory Appl., 1(4), 1046 (2007)
Biswasa PP, Srivastavaa R, Raya S, Samanta AN, Mechatronics, 19(4), 548 (2009)
Ma, M., Chen, H., Findeisen, R. and Allgower, F., Int. J. Innovative Computing, Information and Control, 8(10B), 7083(2012).
Mercangoz M, Doyle FJ, J. Process Control, 17(3), 297 (2007)
Peng C, Han QL, Yue D, IEEE Trans. Control Systems Technology, 21(3), 820 (2013)
Rusli E, Ang S, Braatz RD, Chem. Eng. Educ., 38(3), 174 (2004)
Srinivasarao P, Subbaiah P, Int. J. Computer Applications, 68(12), 21 (2013)
Vijula DA, Devarajan N, Int. J. Engineering Technology, 5(6), 5057 (2013)
Dadhich S, Birk W, European Control Conference (ECC), Strasbourg, France (2014).
Shneiderman D, Palmor ZJ, J. Process Control, 20(2), 18 (2010)
Almurib HAF, Askari M, Moghavvemi M, SICE Annual Conference, September 13-18, Waseda University, Tokyo, Japan (2011).
Gatzke EP, Meadows ES, Wang C, Doyle FJ, Comput. Chem. Eng., 24(2-7), 1503 (2000)
Kundu H, Cohen IM, Dowling DR, Fluid Mechanics, 5th ed., Elsevier, U.S.A. (2011).
Seborg DE, Edgar TF, Mellichamp DA, Doyle FJ, Process Dynamics and Control, 3rd ed., Wiley, U.S.A. (2010).
Edgar TF, Ogunnaike BA, Downs JJ, Muske KR, Bequette BW, Comp. Chem. Eng., 30(10-12), 1749 (2006)
Johansson KH, IEEE Trans. Control Systems Technology, 8(3), 456 (2000)
Abdullah A, Zribi M, Int. J. Comput. Commun., 7(4), 594 (2012)
Alavi SM, Khaki-Sedigh A, Labibi B, Hayes MJ, IET Control Theory Appl., 1(4), 1046 (2007)
Biswasa PP, Srivastavaa R, Raya S, Samanta AN, Mechatronics, 19(4), 548 (2009)
Ma, M., Chen, H., Findeisen, R. and Allgower, F., Int. J. Innovative Computing, Information and Control, 8(10B), 7083(2012).
Mercangoz M, Doyle FJ, J. Process Control, 17(3), 297 (2007)
Peng C, Han QL, Yue D, IEEE Trans. Control Systems Technology, 21(3), 820 (2013)
Rusli E, Ang S, Braatz RD, Chem. Eng. Educ., 38(3), 174 (2004)
Srinivasarao P, Subbaiah P, Int. J. Computer Applications, 68(12), 21 (2013)
Vijula DA, Devarajan N, Int. J. Engineering Technology, 5(6), 5057 (2013)
Dadhich S, Birk W, European Control Conference (ECC), Strasbourg, France (2014).
Shneiderman D, Palmor ZJ, J. Process Control, 20(2), 18 (2010)
Almurib HAF, Askari M, Moghavvemi M, SICE Annual Conference, September 13-18, Waseda University, Tokyo, Japan (2011).
Gatzke EP, Meadows ES, Wang C, Doyle FJ, Comput. Chem. Eng., 24(2-7), 1503 (2000)
Kundu H, Cohen IM, Dowling DR, Fluid Mechanics, 5th ed., Elsevier, U.S.A. (2011).
Seborg DE, Edgar TF, Mellichamp DA, Doyle FJ, Process Dynamics and Control, 3rd ed., Wiley, U.S.A. (2010).